

MES
Experts in MES & Batchcontrol
ImPlant® is a software package developed by Imtech for the automation of batch controlled production processes. Imtech uses the package in different types of production environments such as handling of bulk products, animal feed industry, food and beverage industry, bulk liquid storage, ...
In the automation pyramid, ImPlant® (level 2&3) is situated between ERP (level 4) on the upper side and the PLC-layer (level 1) at the bottom. ImPlant® contains both functionalities in the MES layer (Manufacturing Execution System) and the BCS layer (Batch Control System).
ImPlant® covers all the facets in the plant, ranging from intake of raw materials, transportation of products within the factory, production, packaging and delivery of the finished products. The ImPlant® MES software has a client/server topology. It runs on a MS Windows operating system with a MS SQL Server database. Due to the scalability, ImPlant® can be used in both small and large installations. This may range from a single PC to a system with a server and more than 20 workplaces.

Why ImPlant®
Key performances
Modular
An ImPlant® module has been developed for each step in the production process. These modules can function independently of each other, which makes phased implementation possible. You can therefore spread your investments. Current overviews of stocks and batches in production and finished product can be generated. Contamination control, full track and trace, intake, production and trip planning, OEE (Overall Equipment Effectiveness) and maximisation of production performance are also possible.
Compatible with any ERP system
ImPlant®'s flexibility makes it compatible with any ERP system. So you don't have to worry about your current ERP system, we ensure that we can automate the entire process, without you having to change systems.
Adaptability
Even the smallest details in a form can be configured to fit the needs of the installation. ImPlant® can model most installations with the default functionality. However, the software is extendable and allows the integration of customer-specific forms and features.
Next-level integration
ImPlant® combines the MES functionality with batch control and visualization so that the operator has only one system at his workstation. No more separate screens with each a different user interface in the control room.In many installations, the automation is built with separate systems for MES, batch control and visualization. This results in separated work stations for each level in the control room, each with a different user interface. Because ImPlant® combines MES functionality with batch control and visualization, an operator has to focus only at one system.
Very user-friendly interface.
In each ImPlant® form, a single click on a reference number opens a pop up window showing the related data. For example, in a form showing the details of a production order, one can open a pop-up screen showing the details of the related customer orders or the recipe details or the planned storage silo. The goal is to bring the user directly to the desired data without the need of going through a bunch of menus.
Due to the sophisticated user interface, the best technological choices in the package and the speed of the system, ImPlant® as an operating system is very user-friendly. Moreover, the screens can be configured down to the smallest detail so that they fully meet your needs.
Software package for the automation of batch controlled production processes
Product definition
Management of all master data for raw materials, semi-finished and finished products, including recipes, handling requirements and other parameters necessary for the execution of the production and for quality control. The software provides a great flexibility in terms of settings. Parameters can be set for individually products but also for an entire group of products. This can be an advantage especially for plants with many different recipes and where recipes need to change quickly.
Authorisation
To keep control over which operator can change what data, ImPlant® maintains a user database. All data entry as well as certain actions in the manufacturing process are categorized into functional groups. In the user database, each user is granted rights to one or more of these functional groups.
Stock management
For all materials in the plant, stock details are maintained at the level of silo, tank or warehouse positions. Each raw material batch is uniquely identified on reception and tracked during internal transport up to consumption. For long lasting processes, ImPlant® works with estimated quantities. This allows for a clear view on total stock at all times.
Planning for intake
For goods reception, the ImPlant® MES software provides support for the necessary procedures:
- Registration of all data from the truck (logistic agent/license plate/previous cargo/cleaning certificate ...)
- Necessary tests, sampling, printing of labels
- Registration of gross and tare weight
- Determination of the intake point and storage silo
- Printing of accompanying documents
Production planning & scheduling
The production program starts from the list of customer orders. In the planning screen, the customer orders are presented to the operator in the most production-efficient way, taking the requested delivery date and time into account. This provides a clear view to the operator and helps him with the creation of production orders.
All the production details such as the dosing silos, scales and other equipment are determined automatically and optimally. The production program provides also a prognosis of when a production line will be ready for packaging or delivery.
Quality control
To guarantee quality, standards can be specified for a specific article or article group. When using raw materials or during the production process, samples can be taken automatically or manually. The results of the analyses are stored in the database and compared with the standards. Based on these results, interventions can be made in the process.
- Article standards
- Coupling Masterlab
- Attentionlist quality
- Coupling sample analyzer
Contamination control
At many plants, different types of products are produced on the same production line. Raw materials that are used for the production of one product can be polluting for other products that are to be produced subsequently.
In order to meet GMP compliance for your production process, ImPlant® has the possibility to define polluting components and link them to certain raw materials. In the product master data, one can define for which polluting components a product is sensitive and to what extent. Based on these settings, ImPlant® can calculate at any time whether a particular production order sequence is allowed.
Bulk truck planning
Implant has your entire logistical flow covered. For the delivery of customer orders with bulk trucks, ImPlant® has a module for composing truck trips. The configuration details of all truck compartments is stored in a truck database. Composing a trip is done in a user-friendly way just by selecting a list of customer orders and a few mouse clicks. The determination of the compartment and optimal filling quantity is done automatically based on the product parameters and configuration of the truck. Also, all loading details such as product silo/scale/loading place are determined automatically but can still be adjusted if desired.
This process can be fully automated without any operator intervention, making it extremely useful for fe. the tank terminal business.
Functionalities include:
- Forecast production time
- On Time delivery
- Access control
- Optimization of loading lane occupation
Logistic flow
For points in the logistics flow where intervention of an operator or truck driver is inevitable, ImPlant® offers many possible solutions for the MMI (Man Machine Interface): touch panels, handheld devices (PDAs), barcode scanners, RFID badgereaders ...
Use cases:
- a bulk loading where the truck driver can load his truck fully autonomously. ImPlant® guides the truck driver by means of a PDA.
- the guidance of truck drivers for the intake of raw materials:
- The truck driver gets instructions in his own language on touch panels located at the weighbridge and the intake-points.
- Identification of the trucks drivers is handled with RFID badges or barcode scanners.
BCS (Batch Control System)
One of the components of ImPlant® is a batch control system designed according to the ISA S88 standard for batch processing. A detailed model of the production plant is maintained in this module.
According to the instruction of the production program, the BCS module creates the necessary batches and determines all the production settings. The BCS keeps track of all batches in the production line and communicates with the PLC level where the control of the equipment is carried out
Visualisation of the production process
The background screen of ImPlant® allows you to monitor the state of your entire plan in one sight. The different plant zones are clearly indicated and the different visualization systems indicate the different types of processes. Additional detailed information can be consulted by a single click on an item (batch number, silo number,...).
- Intake and transport: all possible and occupied transport routes are visualised.
- Discontinuous process (weighing/ milling/mixing…): the visualization focuses on the different batches in the process, indicating how far each batch has progressed.
For visualization and operation of machines and equipment, we use standard SCADA software. (Siemens WinCC, Aveva SP).
OEE (Overall Equipment Effectiveness)
The overall efficiency of a production line is crucial to maintain a good competitive position. Especially in a batch-driven process where multiple batches are simultaneously in the production line and are transported from unit to unit, the process efficiency is not always clear.
The OEE functionality of ImPlant® provides the solution to detect any bottlenecks in the process.The system checks at all times if the process runs or is delayed. In case of delay, the cause of the delay is determined and classified per category such as no supply, discharge blocked, process delay, wait for operator, technical failure, ...
If production runs, the system determines which batch in any unit is responsible for using the production time and whether or not this time lies within the predefined limits. Also, the production speed is measured and compared with the norm. All this is presented in the standard OEE way: Availability, Performance, Quality, OEE.
Visualisation
OEE dashboard
The OEE dashboard gives an operator real-time information that allows him to take immediate action if the process is not performing according to the requested standards.
OEE reporting
To measure is to know. The performance data measured during production and displayed in the dashboard are also recorded in the ImPlant®-database and is summarized per hour, per day and per week. This data can be accessed in a user friendly and clear interface.
Diagnostic screen
If you want to analyse the performance of a production line in detail, it is necessary to take a closer look at the relationship between the batches in the individual units in the production line. For this purpose, ImPlant® provides a trending screen which shows on a time basis when units have been occupied by which batch. Here, you can also see which batches are delaying the process at any time..
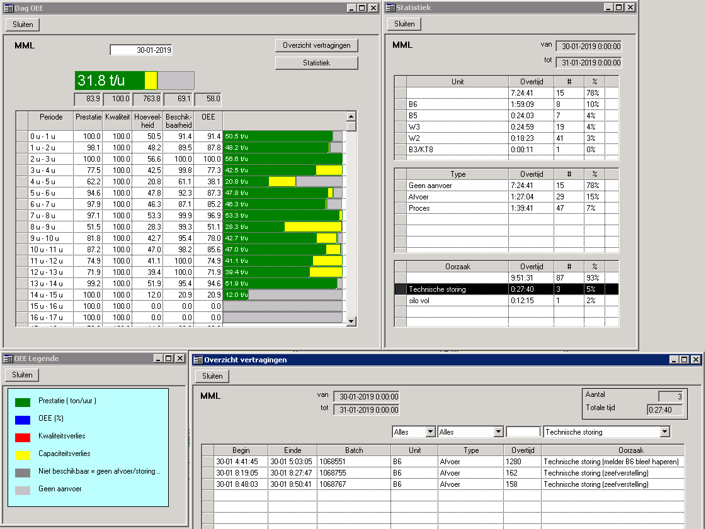
Maintenance program
A maintenance plan can be defined per machine. ImPlant® registers the running hours and the quantities produced of all major equipment in the plant. Based on the hours, ImPlant® generates a maintenance schedule for the technical staff.
MM
In case of any problems or complaints for a certain delivery, ImPlant® will be able to locate all the production details and the individual raw material batches that were used during production.
A query in the other direction is also possible: starting from a suspicious batch of raw material, finding all delivered customer orders that used material from this batch.
Interfacing other systems
Although ImPlant® can function as a standalone system, it can also be equipped with an automatic interface with the ERP level. Imtech has implemented interfaces to several ERP-platforms in the past. All kind of techniques for the exchange of data are available (xml, csv, database, web service ...)
